Schemata Architects embraces rough material finishes for gallery in Seoul
The rough finishes of an existing concrete and brick structure are contrasted by white exhibition spaces at Arario Gallery in Seoul, completed by Japanese studio Schemata Architects.
The gallery is located at the rear of the Space Group Building, a modernist icon in South Korea that houses the Arario Museum.
Designed by architect Kim Swoo-geun, the grey-brick, heritage-listed building was completed in the 1970s and converted into the museum in 2014.
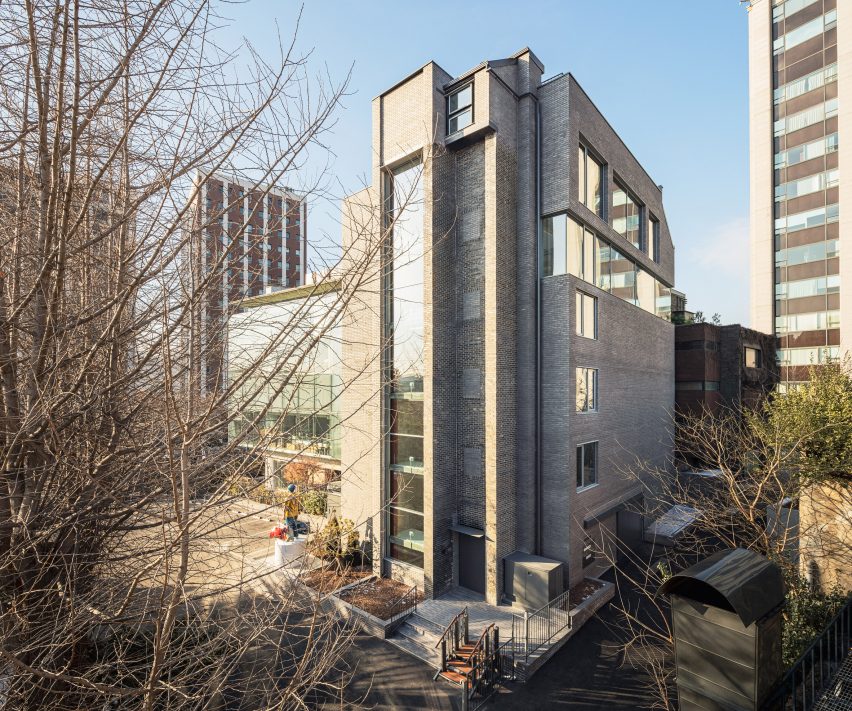
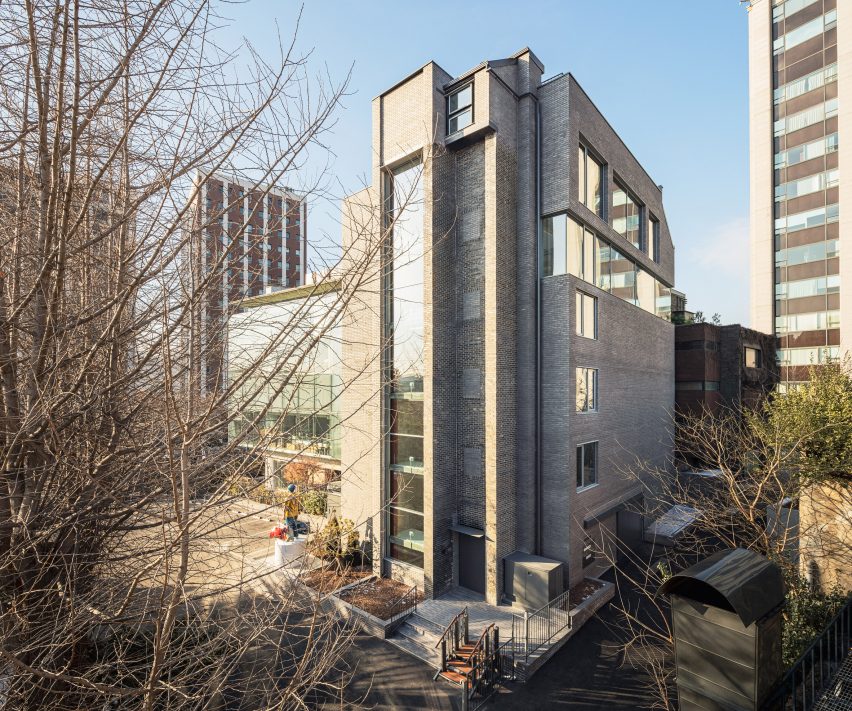
Alongside this building is a glazed extension from the 1990s by architect Jang Se-yang, a student of Swoo-geun, as well as a traditional South Korean home, or hanok, which was relocated to the site when it reopened in 2014.
Amid this architectural backdrop is a brick and concrete structure added to the site in the 1980s, which Schemata Architects was tasked with converting into the Arario Gallery.
“It was a great challenge for me, a Japanese architect, to work on the third building – excluding the hanok – especially after seeing the perfect contrast between the two buildings already created by the master and the disciple,” said Schemata Architects Principal Jo Nagasaka.
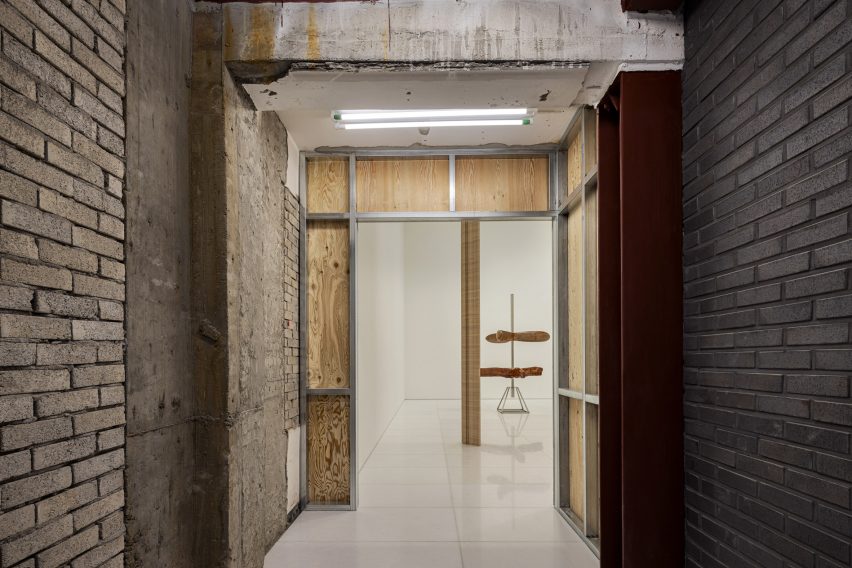
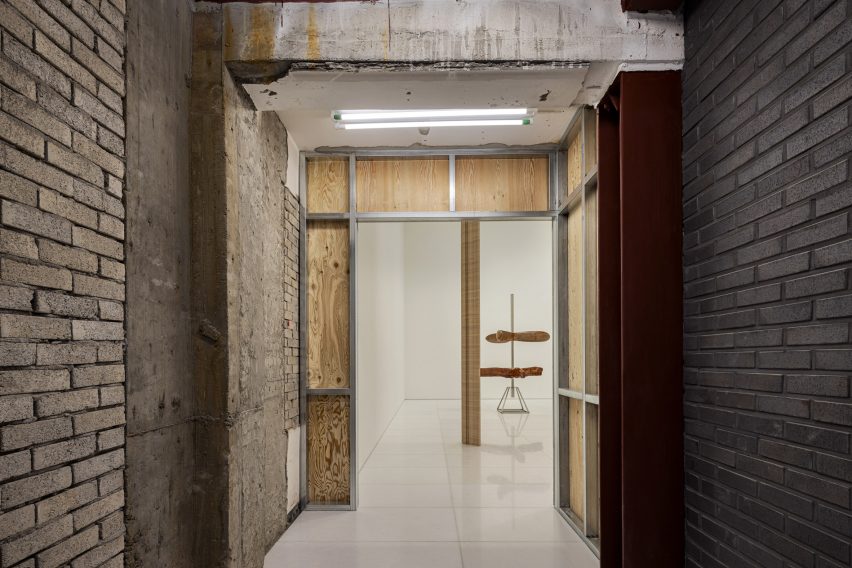
Looking to create a space that “looks unchanged on the outside”, the studio retained the building’s structural frame and dark brickwork, originally chosen to complement the Space Group Building.
“In this context, we thought that inserting another unique feature into the landscape would not be appropriate,” explained Nagasaka.
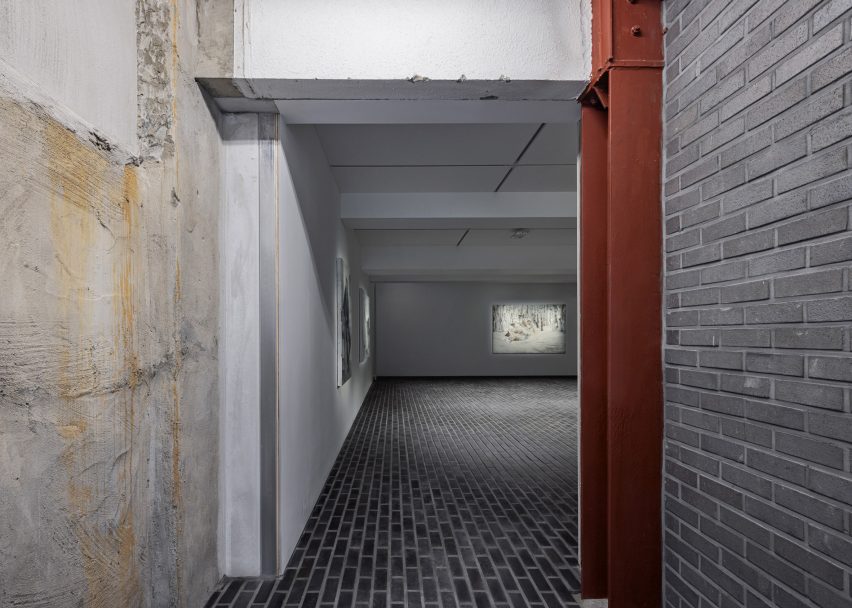
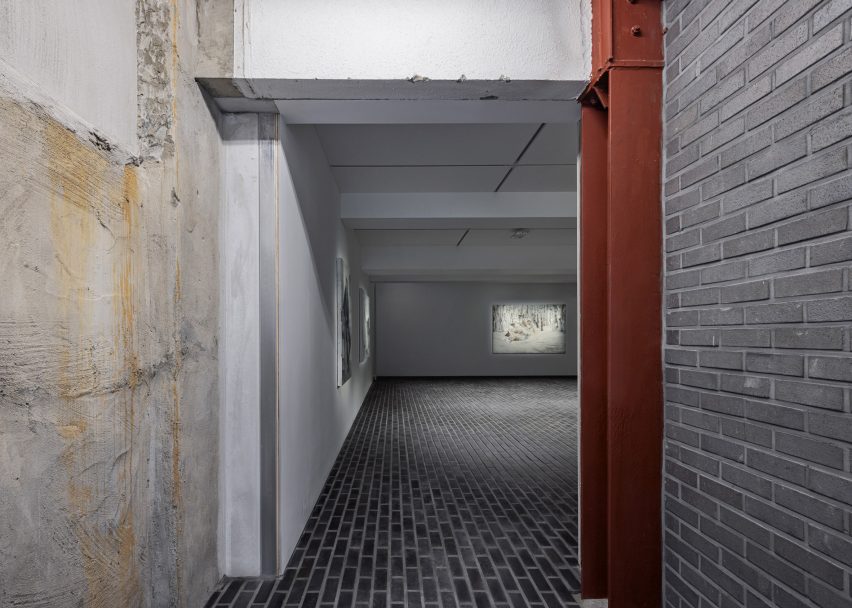
Organised across four floors and a basement level, the white-walled gallery spaces sit alongside the existing staircase, lift, service and storage areas, where the structure’s rough material finishes have been left exposed.
In these more industrial-feeling spaces, walls have been made using plywood on metal frames. Teamed with metal doors and white metal balustrades, they deliberately stand out against the “skeleton” of the existing building.
In the basement, the dark grey brickwork of the adjacent museum is mirrored in a brick floor that extends throughout the space.
On the third floor, sections of the exterior wall were removed to create a full-height glass wall in the VIP area. This looks out towards the nearby Changdeokgung Palace and a surrounding park, also visible through windows in the stairwell.
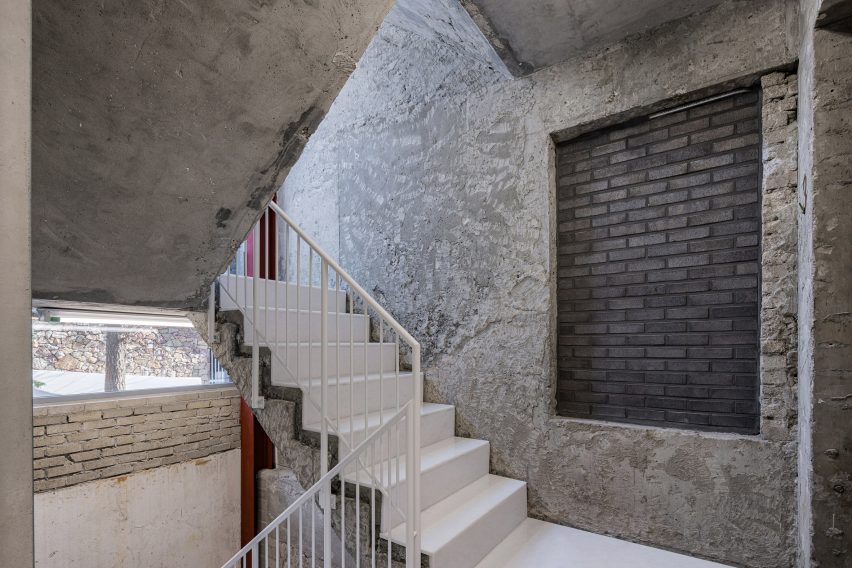
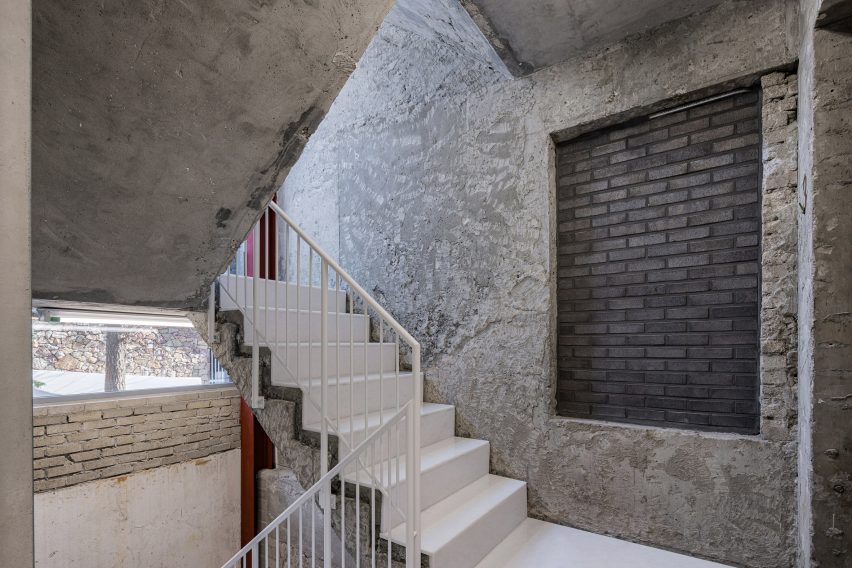
“In this way, we established repetitive patterns where visitors would emerge from the white cube into a skeleton space and see the palace beyond as they ascend to the upper floors,” said Nagasaka.
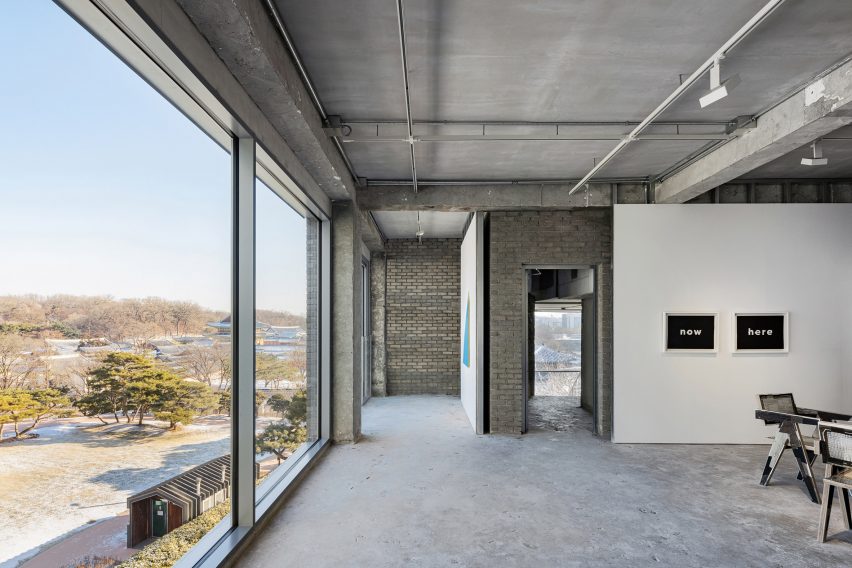
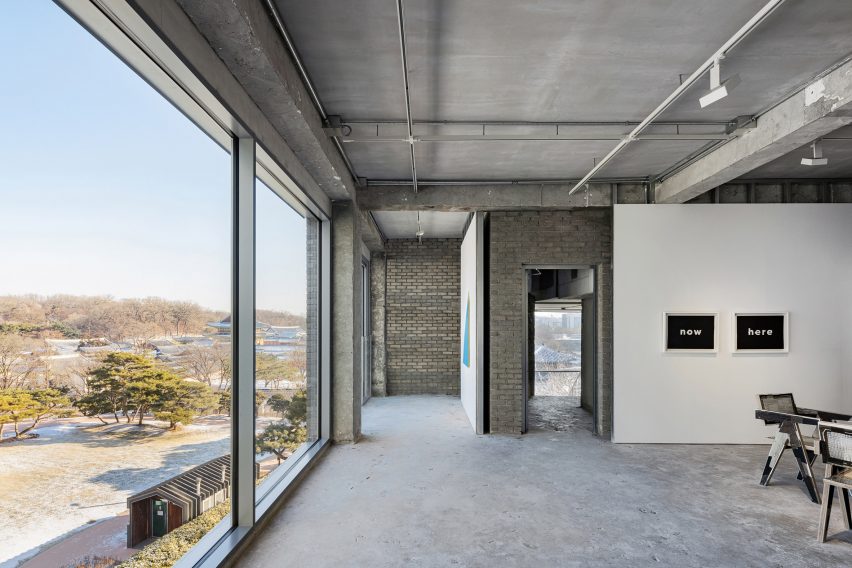
Schemata Architects is a Tokyo-based studio, Founded in 1998 by Nagasaka after he graduated from Tokyo University of the Arts.
Its previous projects include a public bathhouse in Tokyo finished with turquoise tiles and a hillside guesthouse and bar for a home on the coast of an island in the Seto Inland Sea.
The photography is by Yongjoon Choi.