Beauty in the Grain: How a Colorado Mountain Home Was Brought to Life With Redwood Cladding
A home’s materials tell a story of how we live. Nestled in the picturesque mountains of Colorado stands a remarkable testament to sustainable material sourcing. Brought to fruition by Colorado Springs-based architect-engineer Scott Harvey, this mountain home was made to connect with the natural surroundings as an expansive and open retreat. In turn, the project’s redwood cladding reflects a family’s values as they built a home of their own.
A Family Home in the Mountains
Located in the mountains north of Colorado Springs in the town of Monument, this home was made for an active family with five children. The family was hoping for a home that embraced natural light and views out onto the landscape. Working together with builder Palmer Ridge Construction, the team brought the new, 10,538 square-foot home to life with seven bedrooms and expansive glazing. Outside, the home features an unadorned stucco finish and a continuous, seamless band of wood cladding. This warm, redwood band runs non-stop from the exterior through the interior.
The Colorado Mountain Home features an extensive use of redwood from Humboldt Sawmill. Humboldt Sawmill manufactures a full line of redwood and Douglas-fir wood products. Logs are sourced from nearly 450,000 acres of company-owned timberlands, where harvest levels are consistently below the forests’ annual growth rate and harvested trees are replanted. Logs are then processed into lumber.
For this home, the builder had Humboldt Sawmill transport the raw lumber to a dealer in Colorado where it was milled locally to the desired shiplap pattern. Local availability kept the cost within budget. In addition, it was easier to install than tropical hardwoods and no stain was required; only two coats of clear sealer. Redwood, known for its durability, beauty and sustainability, adds warmth to the design and creates a seamless transition from the interior to the exterior of the home.
Sustainable Sourcing
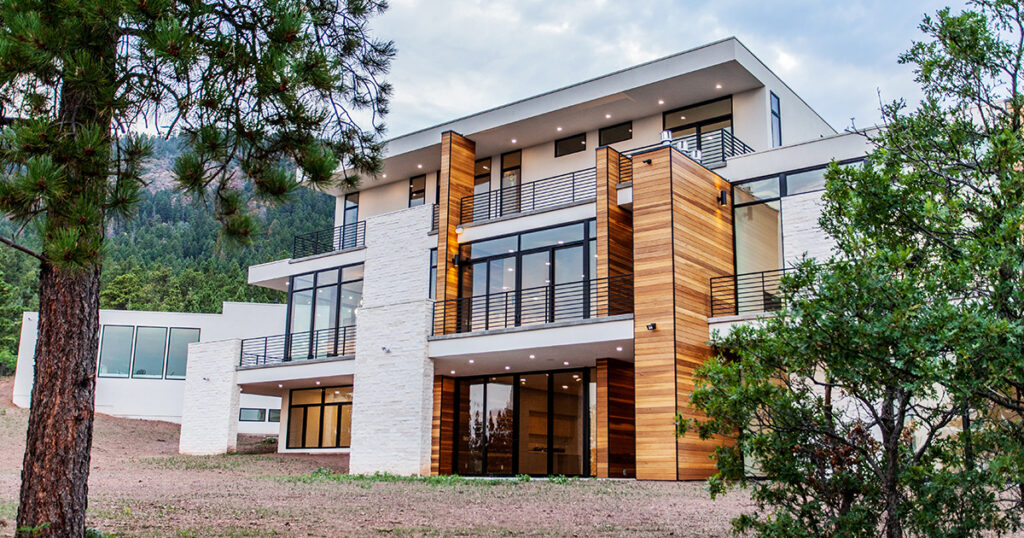
Photo by Kelly Edmondson
What sets this mountain home apart is not just its design but also its commitment to sustainability. The redwood from Humboldt Sawmill was sourced from company-owned Forest Stewardship Council® (FSC® C013133) certified timberlands in Northern California, where it is grown and harvested to the highest environmental standards in the world. FSC certification ensures that products come from forests that provide environmental, social and economic benefits. The FSC Principles and Criteria provide a foundation for all forest management standards globally, including the FSC® US National Standard (v1.0) that guides forest management certification in the U.S.
This commitment to sustainability not only reduces the home’s carbon footprint but also supports the conservation of forests for future generations.
Key Properties of Redwood
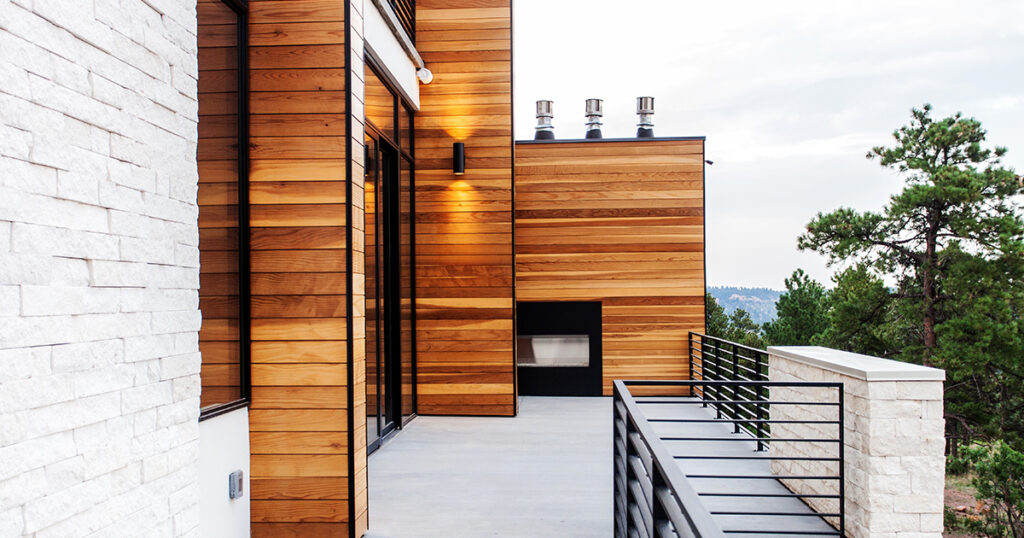
Photo by Kelly Edmondson
Redwood is renowned for its natural beauty and resilience, making it an ideal choice for this mountain home. Redwood is also native to the U.S., not imported. There are several key properties of redwood that make it a preferred building material:
Durability: Redwood heartwood from the center of the tree is naturally resistant to decay and insects, making it an excellent choice for outdoor applications such as siding, decking and fencing. As the team for the Colorado Mountain Home explain, “natural durability through tannins in the redwood heartwood render the wood resistant to termites and decay, an important factor in the home’s mountain environment.”
Aesthetic Appeal: Redwood’s rich color and grain patterns add a touch of elegance and warmth to homes and commercial projects alike. Its natural beauty only enhances over time, developing a patina that adds to the charm of a building.
Sustainability: Redwood is a renewable resource, with the ability to regrow from the stump after harvesting. When sourced from responsibly managed forests, redwood is a sustainable building material that helps reduce the environmental impact of construction.
Workability: Redwood is easy to work with, making it a favorite among architects and builders. It can be easily cut, shaped and installed, allowing for intricate designs and detailing that enhance the overall aesthetics of the home.
Built to Last: A Home for Future Generations
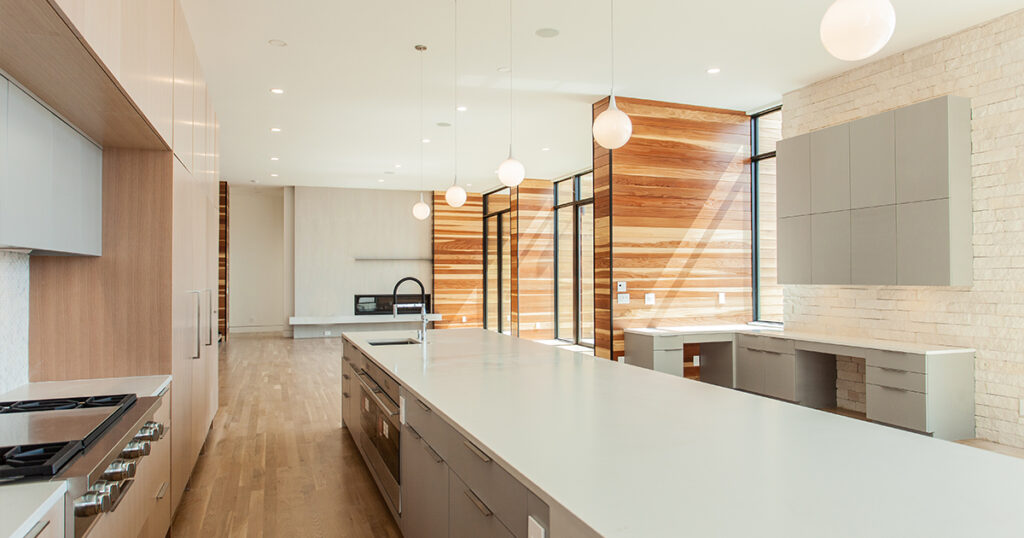
Photo by Kelly Edmondson
At the heart of this Colorado home is the contrast between materials: the natural white Brauer veneer stone and stark white stucco stand out against the warmth of the redwood. Expansive windows open up to views of ponderosa pines and scrub oaks, while inside, the home features white oak flooring and custom cabinets. From these rooms, multiple patios and decks flow together to bring the family outside and create connections to their surroundings.
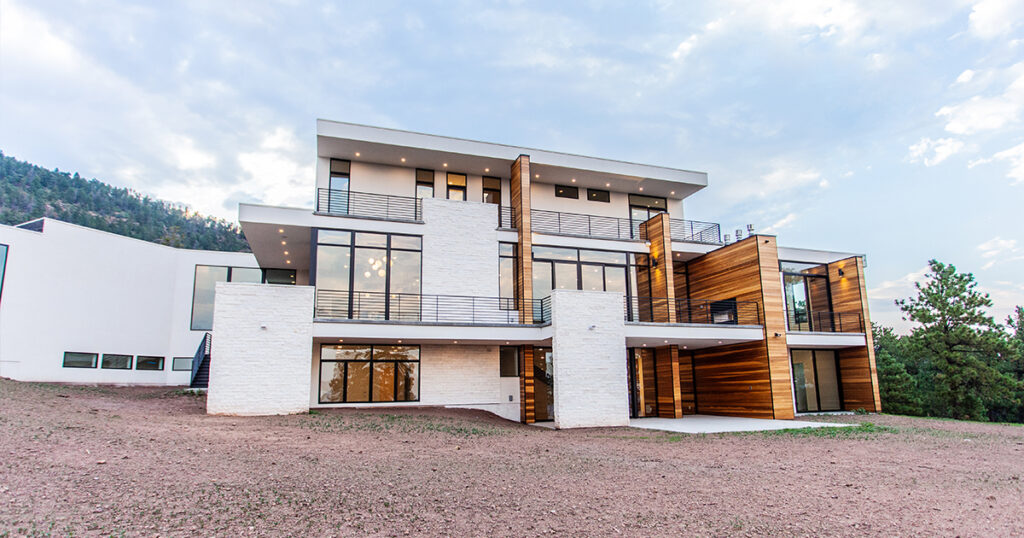
Photo by Kelly Edmondson
The Colorado mountain home stands as a testament to the harmonious relationship between nature and design. Through the use of Humboldt Sawmill’s redwood sourced from responsibly managed forests, this home not only showcases the beauty and durability of this remarkable material but also highlights the importance of working with the right manufacturers and builders. Today, the home tells a story of family, warmth and connectedness through its details and construction.
To learn more about how you can harness the unique qualities of redwood for your next project, reach out to the experts at Humboldt Sawmill.